Each year, a high number of workplace accidents result from maintenance and non-production tasks carried out on machinery and equipment.
That’s why it’s essential to plan and supervise all maintenance, installation, decommissioning, repair, servicing, adjusting, calibrating and cleaning activities on machinery and equipment in the workplace.
Typically, fatalities and injuries related to these tasks result from:
- an over-reliance on workers’ specialist skills
- a reluctance to supervise workers with specialist knowledge
- inadequate completion of JHA’s, JSEA’s or Take Fives
- failure to ensure contractors are complying with health and safety requirements
- failure to isolate machinery and equipment prior to undertaking activities
- prioritising production needs over health and safety.
While employers, managers and supervisors have specific responsibilities when it comes to eliminating or reducing risks to workers – everyone in the workplace should play a role in making sure activities are done safely.
Whatever industry you work in – if you have machinery and equipment, the information contained here is relevant to you
Planning maintenance and non-production tasks
Working on plant to keep it running at its optimum performance level can be complex. Often workers maintaining or repairing plant face different hazards to those actually operating plant, so it’s essential that these tasks are carefully planned to eliminate or reduce risks.
Contractor management
Maintenance and non-production tasks are commonly performed by contractors, so planning to ensure their safety is a must.
It’s essential that contractors are aware of the safety procedures in place, understand how these safety procedures work and follow them correctly.
Isolating plant
Plant must be isolated before any maintenance or repair work is carried out on machinery or equipment. Failure to isolate or de-energise plant can have disastrous consequences, including serious injury or death. It is crucial that machinery and equipment isolation procedures are followed or developed for each task on each item of plant and that these are understood and followed by workers.
Working on energised plant
There are significant risks associated with undertaking maintenance and repair work on energised plant. Plant should always be isolated and locked out where reasonably practicable to do so.
Where it is not reasonably practicable to isolate plant there are a number of steps and safety precautions that need to be put in place to protect workers. Ensure you review & follow the site procedures prior to commencing any works.
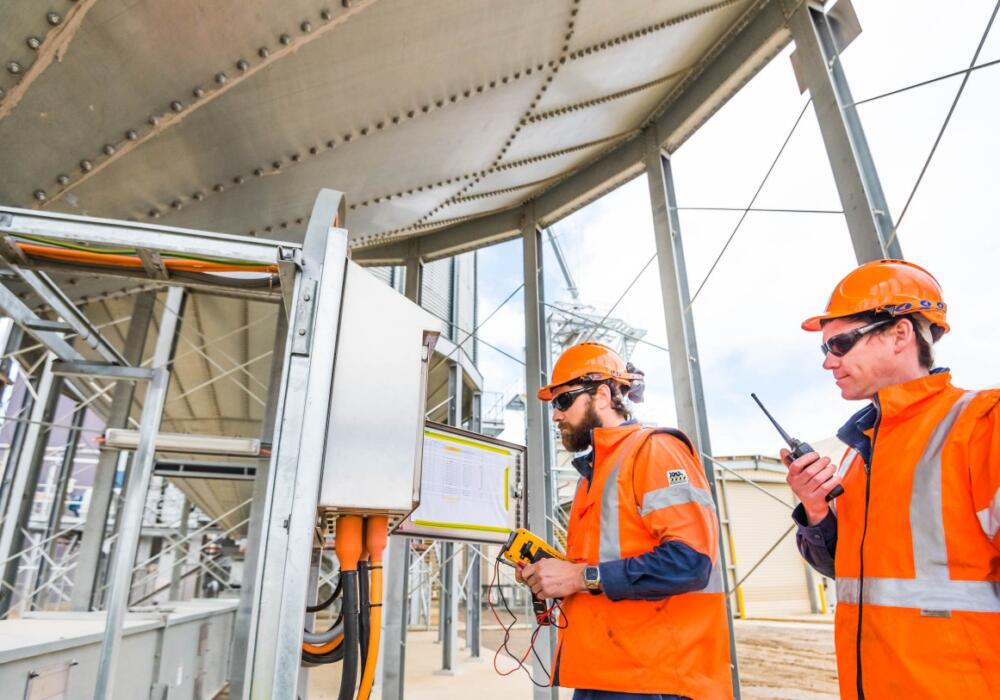